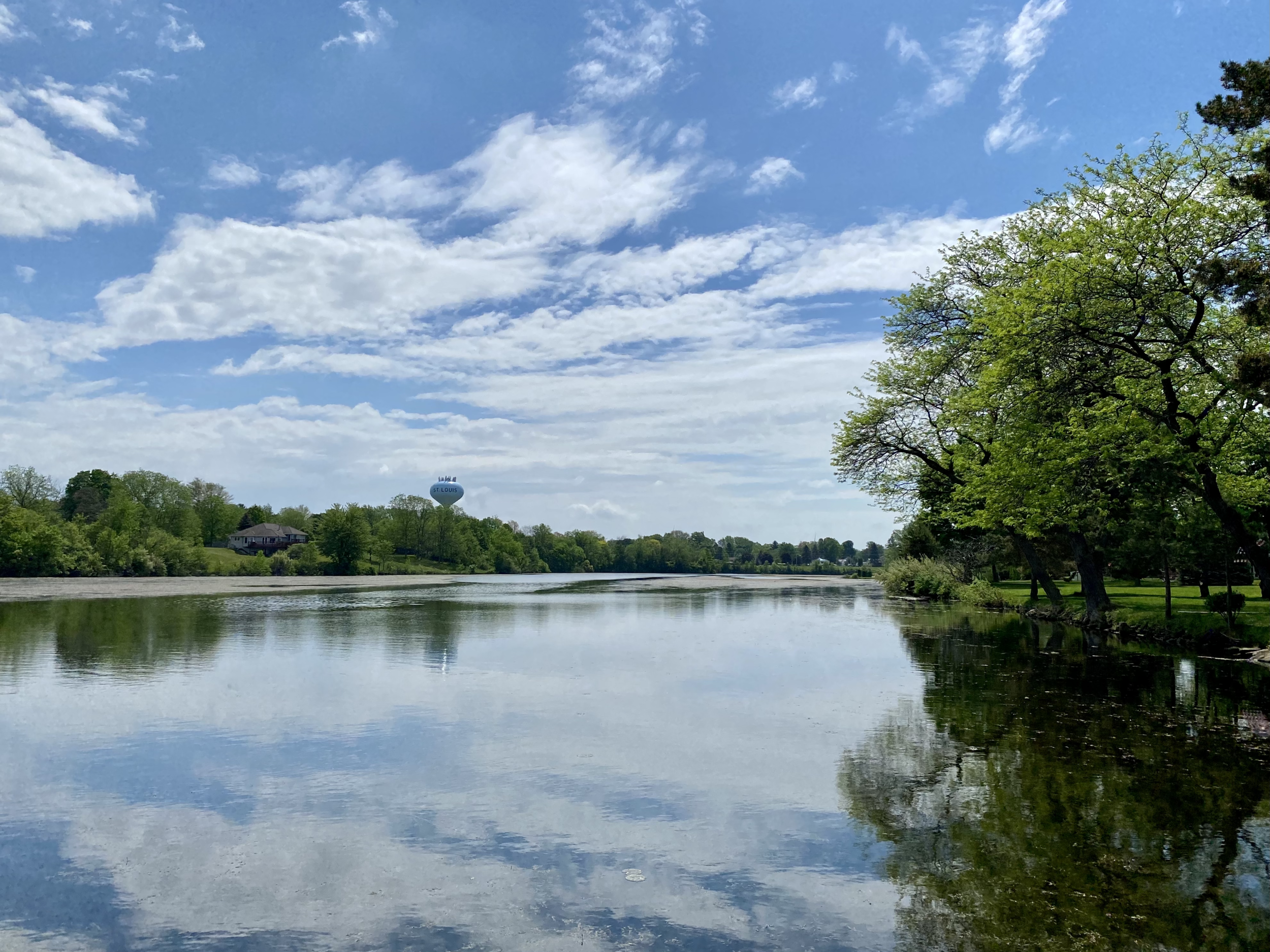
Restoring the Pine River for future generations
The Pine River Superfund Citizen Task Force works to inform the public of the environmental and human health remediation work in the Pine River watershed in central Michigan.
This is the official website for the Pine River Superfund Citizen Task Force. We are a non-profit organization established in 1998 to provide advice to U.S. Environmental Protection Agency in its effort to remediate three U.S. Superfund sites in the Pine River watershed in the middle of Michigan’s lower peninsula.
Why we are here.
The Pine River watershed in northern Gratiot County, Michigan has been an environmentally stressed community for more than a century, experiencing cycles of both growth and decline as a result of resource exploitation. We are working to restore and restore the river for the health of the river and the community that calls the river home.
The Problem
The origin of our work is the contamination thoughtlessly introduced into the environment by the former Michigan Chemical/ Velsicol Chemical plant on the Pine River in St. Louis, Michigan. This photo from about 1970, shows the company's careless dumping into the river. Note that in winter, they melted the ice in the river.
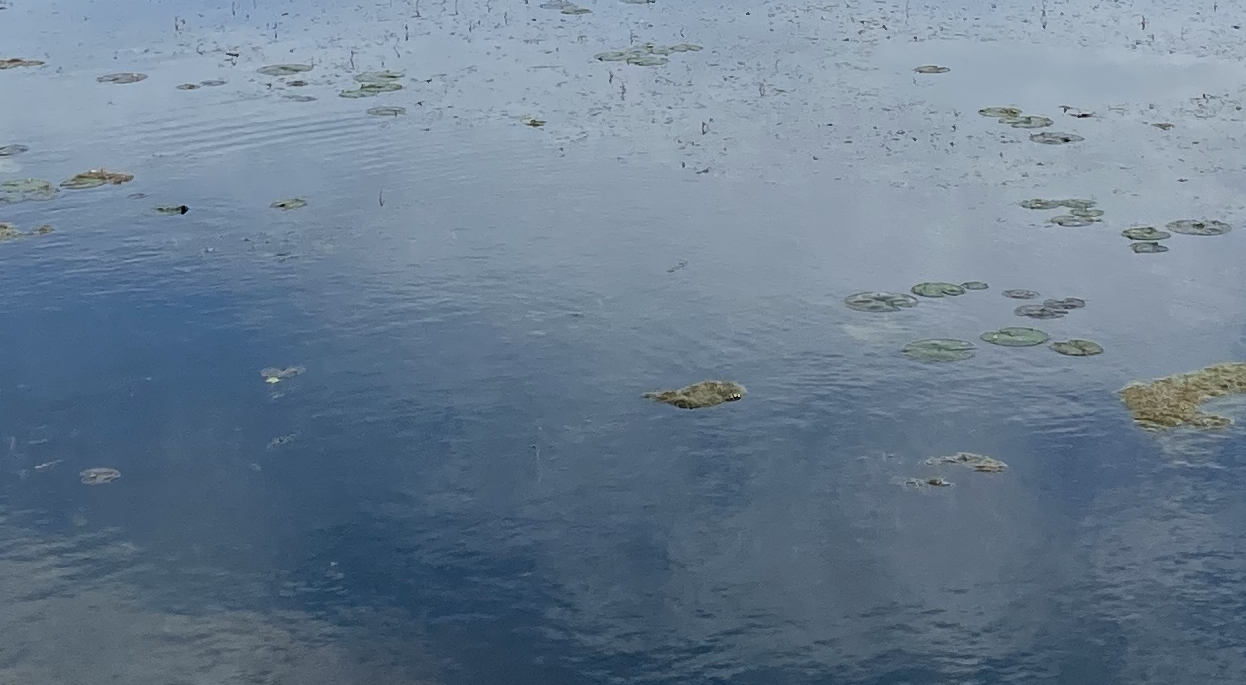
“It is much better to prevent than to cure, and so much easier to foresee future harm and avoid it rather than have to get rid of it after having fallen prey”
— Dr. Bernardino Ramazzini
the “father of occupational medicine”
Let’s work together to restore the Pine River to its pristine natural beauty. Let’s finally resolve human health concerns growing from the contamination and provide clinical responses for verified health problems.
Sign up to join our mailing list. We will let you know about upcoming meetings and events.